How we make Your Biosofa
Let's walk through our manufacturing process step by step.
Everything we produce is handcrafted in our Workshops on lake Como in Italy.
We teach our methods in Schools and Universities.
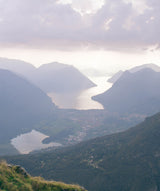
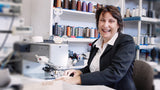
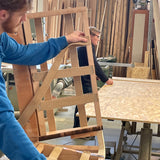
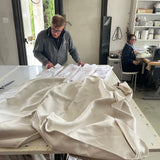
1 - Concept and Prototyping
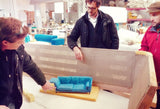
Sometimes, designers will build a miniature model to clarify what they are looking for in terms of proportions. Here, ddp studio are presenting the first model of Casquet.
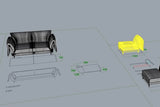
Once the designers agree on the proportions with our production team, our product developers will make a computer 3D model. This is also the base for calculating textile usage and cutting patterns for sewing.
Furniture making is a collaborative process. Only when everybody involved in the development of the new sustainable sofa gives a green light, the proper production can start.
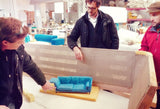
Sometimes, designers will build a miniature model to clarify what they are looking for in terms of proportions. Here, ddp studio are presenting the first model of Casquet.
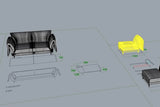
Once the designers agree on the proportions with our production team, our product developers will make a computer 3D model. This is also the base for calculating textile usage and cutting patterns for sewing.
Furniture making is a collaborative process. Only when everybody involved in the development of the new sustainable sofa gives a green light, the proper production can start.
2 - Artisanal Woodwork: Crafting the Backbone
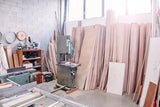
Biosofa products never include chipboard or MDF, and our specialized team preserves the woodworking tradition of our region in the north of Italy, Brianza.
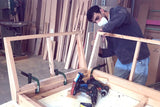
We have a true hands-on approach as wooden pieces are cut, sanded, measured, and assembled under the skilled guidance of our head carpenter Fabio Solenne. Our workshops always carry the perfume of wood.
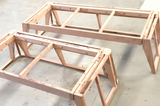
Every frame is checked before we start our next steps in building the sofa.
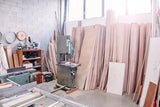
Biosofa products never include chipboard or MDF, and our specialized team preserves the woodworking tradition of our region in the north of Italy, Brianza.
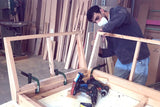
We have a true hands-on approach as wooden pieces are cut, sanded, measured, and assembled under the skilled guidance of our head carpenter Fabio Solenne. Our workshops always carry the perfume of wood.
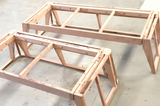
Every frame is checked before we start our next steps in building the sofa.
3 - Comfort without Plastic: Jute and Metal Springs
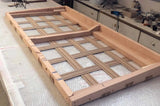
The elastic base layer incorporates vertical and horizontal stripes of jute to enhance flexibility and comfort.
As opposed to plastic, Jute will not stretch over time, ensuring an even seating over decennies.
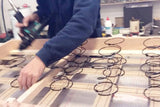
Between the belts, we insert demagnetised steel springs and finish with another cri-cross layer of Jute.
We also propose options that are metal-free.
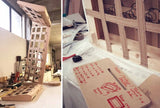
The final touch is a pure jute cloth covers that will cover the entire web of belts and springs, ensuring a smooth foundation for the next layers.
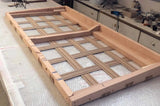
The elastic base layer incorporates vertical and horizontal stripes of jute to enhance flexibility and comfort.
As opposed to plastic, Jute will not stretch over time, ensuring an even seating over decennies.
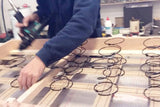
Between the belts, we insert demagnetised steel springs and finish with another cri-cross layer of Jute.
We also propose options that are metal-free.
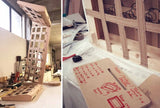
The final touch is a pure jute cloth covers that will cover the entire web of belts and springs, ensuring a smooth foundation for the next layers.
4 - Cotton Felt and Latex Padding

Our 100% Natural Latex is delivered in large blocks and we cut it down to the needed sizes in the correct height and length using our large scale vertical saw.
This process takes experience and craftsmanship, as the material is very soft and any push or pull in the wrong direction will result in an uneven cut.
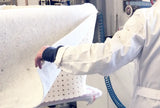
The layering process allows our artisans to sculpt the sofa, especially when crafting designs with rounded or soft lines.
By carefully applying the different layers we can sculpt the sofa as envisioned in the first sketches. This really is the difficult part, and here all the workmanship of our artisans plays out.
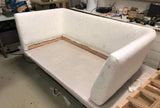
To protect the latex cells from dust and damage, we apply an extra protective layer of recycled cotton felt. This layer will also provide a firmer feel and keep the relatively wobbly latex foam compact and in shape.
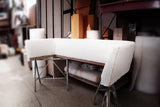
Last comes a pure cotton textile layer. This will support the final textile cover, ensuring a seamless finish without creases or folds.

Our 100% Natural Latex is delivered in large blocks and we cut it down to the needed sizes in the correct height and length using our large scale vertical saw.
This process takes experience and craftsmanship, as the material is very soft and any push or pull in the wrong direction will result in an uneven cut.
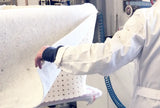
The layering process allows our artisans to sculpt the sofa, especially when crafting designs with rounded or soft lines.
By carefully applying the different layers we can sculpt the sofa as envisioned in the first sketches. This really is the difficult part, and here all the workmanship of our artisans plays out.
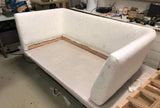
To protect the latex cells from dust and damage, we apply an extra protective layer of recycled cotton felt. This layer will also provide a firmer feel and keep the relatively wobbly latex foam compact and in shape.
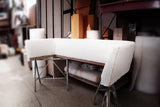
Last comes a pure cotton textile layer. This will support the final textile cover, ensuring a seamless finish without creases or folds.
5 - Tailoring the Textiles
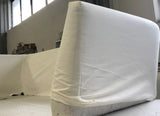
The addition of a white cotton undercover will support the final textile cover to run smoothly and prevent creases or folds.
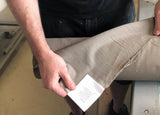
Each textile has its own little features and challenges. With velvet for example, the lay of the soft surface will reflect the light differently depending on the direction of the weave.
So we need to take that into account when cutting our pieces, they are what we call directional. The same goes for patterns.
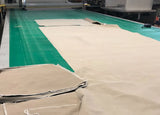
With the 3D model that we have created early in the process, we’re now able to get the exact cuts for the textiles.
We pass the shapes into our dedicated cutting program which is linked to our automated large scale cutting table. With its size of 3 x 8 meters and a movable arm we’re able to easily and precisely cut all the materials.
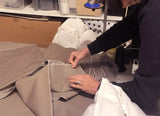
Once all textile pieces are cut, our seamstresses clean them and assemble the covers while borders, zippers and threads are matched to the textile color.

Sewing a sofa is hard work. All parts are heavy, and need to be assembled exactly. Often, the final stitching is very visible and must be absolutely perfect to pass quality control.
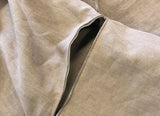
Zippers, buttons, closures and decorative seams are the last steps in the Biosofa sewing process.
We do not use Velcro or any other plastic fastenings. So this step may take a bit longer, until everything aligns perfectly.
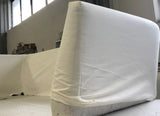
The addition of a white cotton undercover will support the final textile cover to run smoothly and prevent creases or folds.
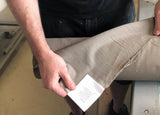
Each textile has its own little features and challenges. With velvet for example, the lay of the soft surface will reflect the light differently depending on the direction of the weave.
So we need to take that into account when cutting our pieces, they are what we call directional. The same goes for patterns.
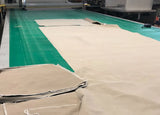
With the 3D model that we have created early in the process, we’re now able to get the exact cuts for the textiles.
We pass the shapes into our dedicated cutting program which is linked to our automated large scale cutting table. With its size of 3 x 8 meters and a movable arm we’re able to easily and precisely cut all the materials.
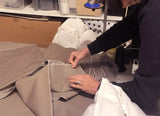
Once all textile pieces are cut, our seamstresses clean them and assemble the covers while borders, zippers and threads are matched to the textile color.

Sewing a sofa is hard work. All parts are heavy, and need to be assembled exactly. Often, the final stitching is very visible and must be absolutely perfect to pass quality control.
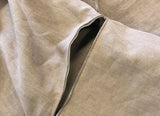
Zippers, buttons, closures and decorative seams are the last steps in the Biosofa sewing process.
We do not use Velcro or any other plastic fastenings. So this step may take a bit longer, until everything aligns perfectly.
6 - Backrests and Cushions
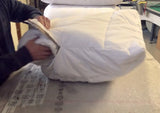
The backrest will be made from pure feathers (or a vegan alternative) and is actually a cushion within a cushion. This method guarantees support with maximum softness.
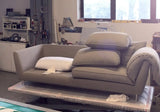
The technique we use to keep all the soft material in place is to sew it into air compartments. Imagine a system similar to that of a down jacket.
Rows of fluff or feathers add up to a sort of blanket that will then be shaped further.
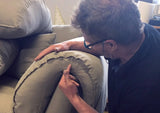
The inner layer for the seating cushion is a latex layer featuring 10 to 20 centimetres of thickness. Once again, using our 100% natural latex!
These latex pieces will finally be covered by a feather chamber cushion, much like the outer ones on the backrest.
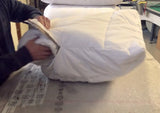
The backrest will be made from pure feathers (or a vegan alternative) and is actually a cushion within a cushion. This method guarantees support with maximum softness.
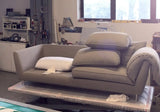
The technique we use to keep all the soft material in place is to sew it into air compartments. Imagine a system similar to that of a down jacket.
Rows of fluff or feathers add up to a sort of blanket that will then be shaped further.
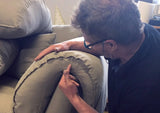
The inner layer for the seating cushion is a latex layer featuring 10 to 20 centimetres of thickness. Once again, using our 100% natural latex!
These latex pieces will finally be covered by a feather chamber cushion, much like the outer ones on the backrest.
7 - Quality Control
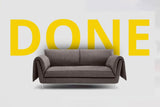
We double-check all measurements and features.
We also make a thorough Video and Photographic documentation for our Clients, so they can go through every detail and witness the craftmanship. We show all details, including the undeside and other hidden sides, to make sure all is perfect.
Only then the Customer gives the go-ahead for the delivery.
The Biosofa is now a masterpiece, ready to be shipped and bring joy to your space.
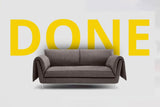
We double-check all measurements and features.
We also make a thorough Video and Photographic documentation for our Clients, so they can go through every detail and witness the craftmanship. We show all details, including the undeside and other hidden sides, to make sure all is perfect.
Only then the Customer gives the go-ahead for the delivery.
The Biosofa is now a masterpiece, ready to be shipped and bring joy to your space.